Advancements in Precision Hardware Manufacturing Technique
Advancements in Precision Hardware Manufacturing Techniques
The evolution of CNC (Computer Numerical Control) machines has revolutionized precision hardware manufacturing, delivering precision measured in microns. These machines have dramatically enhanced manufacturing accuracy, enabling production of components with complex geometries and tight tolerances. CNC technology has drastically reduced human error by automating intricate tasks and ensuring consistent quality across production batches.
CNC machines form the backbone of modern precision manufacturing, facilitating the creation of intricate designs and ensuring uniformity across entire production runs. Their reliance on CAD (Computer-Aided Design) and CAM (Computer-Aided Manufacturing) technologies further underscores their importance. These tools enable designers to craft complex designs digitally, which CNC machines then convert into tangible products with remarkable precision.
Key technological advancements such as multi-axis machining have further refined CNC machine capabilities. Multi-axis CNC machines, ranging from three to twelve axes, provide manufacturers with flexibility and precision, essential for producing detailed parts like turbine blades. Such advancements are not just about efficiency; they also allow for the intricate design capabilities needed in advanced manufacturing sectors.
Importance of Automation in Precision Manufacturing
Automation plays a crucial role in precision manufacturing by enhancing accuracy and minimizing human error. Before automation was widely integrated into manufacturing processes, defect rates were notably high. Studies have shown that defect rates can decrease by over 70% when automation is applied, as automated systems provide consistent and precise performance that surpasses human capabilities. This precision is particularly significant in industries requiring exact measurements, such as aerospace and medical device manufacturing.
In addition to improving accuracy, automation significantly reduces downtime in manufacturing operations. Automated machinery, such as robotic arms, streamline processes by performing repetitive tasks more efficiently than human workers. For example, automated systems can work continuously without fatigue, which drastically reduces the time lost due to manual error or slowdowns caused by human involvement. As a result, manufacturers experience increased productivity and operational efficiency, enabling them to fulfill customer demands more swiftly and reliably. This transformation underscores the critical role of automation in modern manufacturing, facilitating seamless and efficient production environments.
Multi-Axis Machining in Modern Manufacturing
Multi-axis machining significantly enhances manufacturing processes by offering improved precision and the ability to handle complex geometries. With this technology, manufacturers can produce intricate pieces in fewer setups, reducing the likelihood of errors and the need for multiple transitions between machines. By consolidating tasks, manufacturers gain efficiency, saving time and resources. Moreover, multi-axis machines, which can operate along several axes simultaneously, allow for the seamless creation of complex parts like turbine blades and intricate molds. This versatility is crucial in modern manufacturing, where precision and reduced production times are increasingly essential.
The applications of multi-axis machining extend across various industries, particularly in sectors requiring complex designs, such as aerospace and automotive. In aerospace, the demand for parts with stringent tolerances and unique shapes is constant, making multi-axis machining indispensable. Likewise, the automotive industry relies on this technology to produce components with sophisticated geometries essential for modern vehicle designs. Using multi-axis machining ensures these industries maintain high standards of precision and efficiency, which are vital for maintaining competitiveness in today's market. Through these applications, multi-axis machining serves as a cornerstone for innovation and quality advancement in precision manufacturing.
Material Innovations Shaping the Industry
In recent years, there has been a notable shift towards lightweight materials in the manufacturing industry, which is transforming how precision components are produced. Materials such as composites and aluminum alloys are at the forefront of this shift, offering significant benefits like reduced energy consumption during transportation. These materials possess a high strength-to-weight ratio, making them ideal for industries demanding efficiency, such as automotive and aerospace. For example, the use of aluminum in vehicle construction not only decreases weight but also enhances fuel efficiency and performance.
Concurrently, the rise of eco-friendly materials in precision manufacturing has provided new pathways for sustainable innovation. There is a growing interest in biodegradable materials and sustainably sourced raw materials, as manufacturers are increasingly conscious of their environmental impact. Precision parts made from eco-friendly materials, such as natural fiber composites, not only reduce reliance on non-renewable resources but also decrease the carbon footprint associated with manufacturing processes. This trend aligns with global efforts toward sustainability, enabling manufacturers to meet the rising consumer demand for greener solutions while maintaining high performance standards.
Cutting-Edge Products in Precision Hardware
Precision hardware is advancing rapidly with products designed for specific applications in diverse industries. One such product is the excellent quality dowel pin, which finds significant applications in furniture and machinery settings. These pins are essential for accurate alignment and secure joining. Applications extend to cabinets, sofas, and various industrial machinery, ensuring precise positioning and stability in joints.
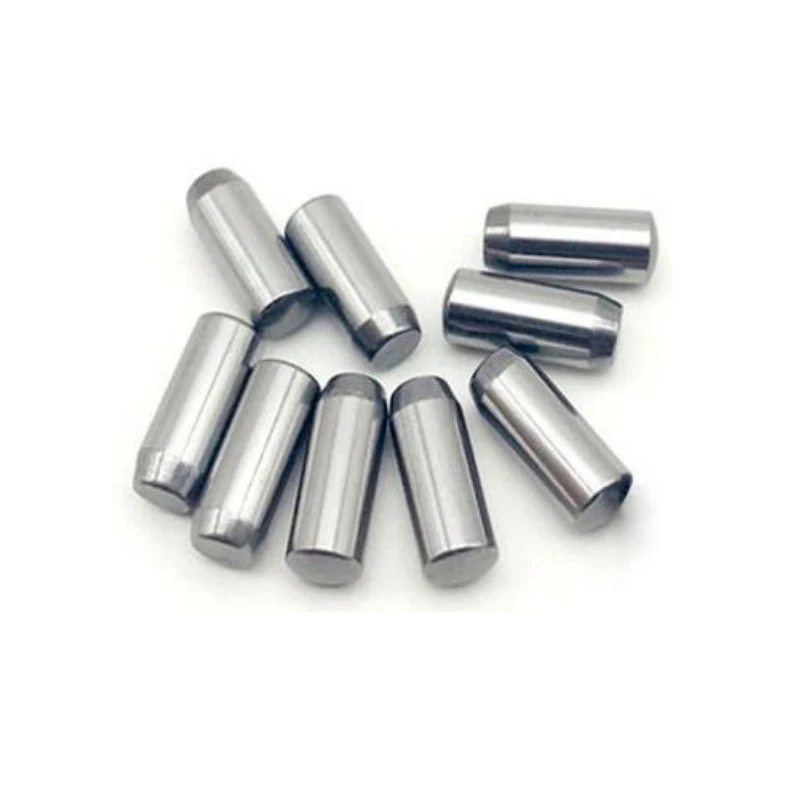
Another sophisticated precision hardware product is the ball spring plunger, commonly employed in adjustable locking mechanisms and fixtures. These plungers allow for efficient and reliable adjustments, making them indispensable in applications requiring repeatable precision and flexibility. They are essential for securely locking parts in place, thus maintaining positional stability while allowing for the swift reconfiguration of fixtures as needed.
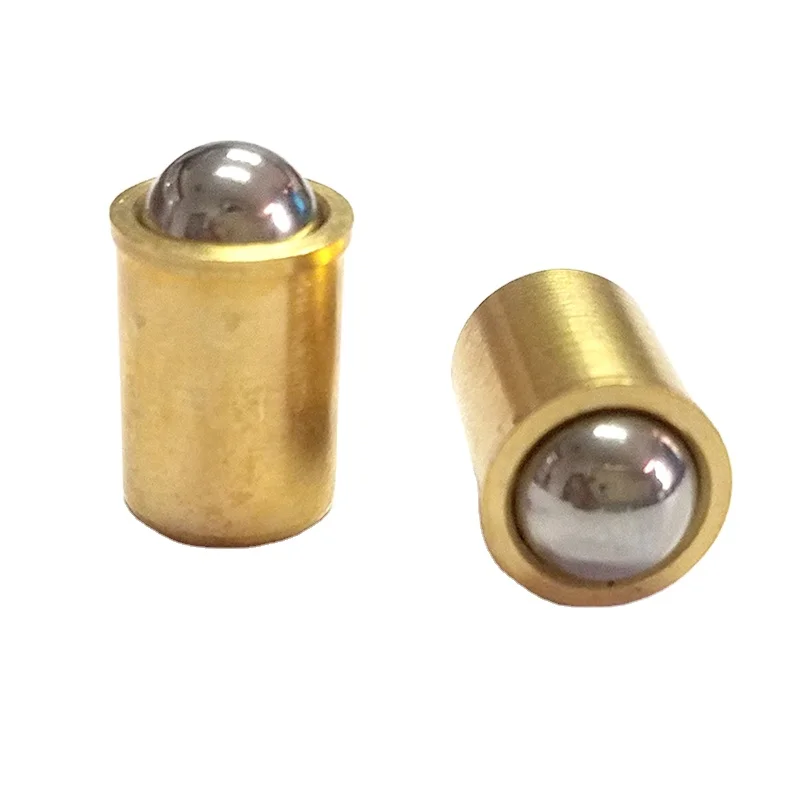
Finally, spring-loaded guide plungers play a crucial role in facilitating smooth linear movement in automation settings. These guide plungers are key in processes that require steady linear motion, such as conveyor systems, robotic arms, and other automated machinery. By ensuring seamless transitions and maintaining alignment, these plungers enhance the efficiency and reliability of automated systems.
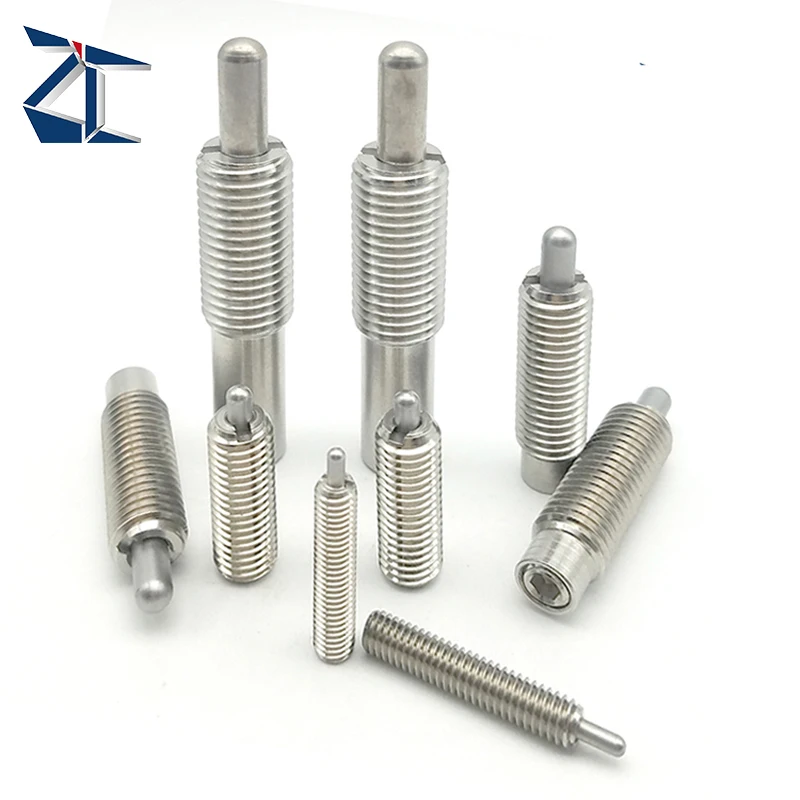
These innovative products underscore a growing trend in adopting specialized hardware to boost operational precision and adaptability in various industrial and consumer applications.
Future Trends in Precision Hardware Manufacturing
The future of precision hardware manufacturing is heavily influenced by the principles of Industry 4.0, which encompasses smart manufacturing and Internet of Things (IoT) integration. These innovations are dramatically enhancing production efficiency by automating processes and providing real-time data analytics for better decision-making. The adoption of technologies such as robotics, artificial intelligence, and cloud computing supports seamless integration between software and hardware, fostering a more cohesive manufacturing system. As a result, companies are not only minimizing errors but also achieving higher precision and consistency in their products.
Furthermore, innovations in customization and flexibility are shaping the precision hardware landscape. On-demand manufacturing is becoming increasingly viable due to the growing consumer preference for personalized products. This shift is driving manufacturers to alter product designs to align with consumer demands, leveraging advanced production techniques to accommodate small batch productions efficiently. The impact of customization is evident in various industries, from automotive to consumer electronics, as it allows for tailored product features that cater to specific consumer requirements. Such trends are expected to continue as market dynamics evolve, emphasizing the need for adaptability and responsiveness in manufacturing processes.