Exploring the Versatility of Ball Rollers in Material Handling
Understanding the Versatility of Ball Rollers in Material Handling
Ball rollers, also known as ball transfer units, are a fundamental component in material handling systems. These devices are designed with a spherical ball that rotates within a casing, allowing objects to move in any direction with minimal friction. The functionality of ball rollers is enhanced by components like shoulder bolts, which secure them in place, and pull handles for manual adjustments. These elements contribute to a seamless operation, enabling easy maneuverability of materials across various platforms.
The adaptability of ball rollers is evident in their diverse applications. They effectively handle different materials, offering solutions across industries such as manufacturing, logistics, and even food processing. Ball rollers can accommodate various environments, from warehouse floors to refrigerated units, ensuring smooth transit of goods. Their ability to work with a range of weights and dimensions makes them indispensable in scenarios requiring both efficiency and versatility. This adaptability underscores their role in optimizing operations, whether in assembly lines or complex conveyor systems, enhancing productivity while minimizing the need for manual handling.
Applications of Ball Rollers in Various Industries
Ball rollers are integral components in manufacturing and assembly lines, significantly enhancing productivity and efficiency. These rollers facilitate the smooth transfer of materials between workstations, minimizing downtime and bottlenecks. By allowing components to be moved with ease, they optimize workflow efficiency, making operations in these sectors more streamlined and organized.
In the aerospace and automotive industries, ball rollers play a crucial role due to the precision required. These sectors demand meticulous handling of parts, and ball rollers provide the necessary control and accuracy for assembling complex components. Their ability to handle heavy materials with precise positioning makes them indispensable in these industries.
In the food processing and packaging industry, the use of ball rollers is significant for maintaining hygiene standards and ensuring material compatibility. These rollers not only support efficient handling and packaging but are also designed to meet stringent cleanliness requirements. Their adaptability to various materials ensures that they are suitable for use in environments where hygiene is paramount, contributing to the safe and efficient processing of food products.
Key Benefits of Using Ball Rollers in Material Handling
Ball rollers significantly enhance mobility and maneuverability in material handling operations, facilitating smoother and more efficient processes. These devices allow for omnidirectional movement, reducing the need for manual interventions and enhancing workflow efficiency. According to industry studies, implementing ball rollers in material handling can achieve up to a 30% reduction in handling time, which translates into substantial time savings and improved productivity.
In addition to reducing handling time, ball rollers contribute to a decrease in wear and tear on products. By minimizing friction during movement, they can prolong the lifespan of equipment and materials. High-quality ball rollers ensure longevity, leading to cost savings over time. Companies that have integrated ball rollers report significant reductions in maintenance costs, further emphasizing their value as a long-term investment.
Moreover, incorporating ball rollers into operations can enhance processing speed, enabling businesses to manage higher volumes with greater efficiency. For instance, assembly lines equipped with ball rollers often experience smoother transitions between stations, minimizing delays and bottlenecks. Examples from industries such as automotive and aerospace highlight how integrating ball rollers can improve processing times and contribute to higher output levels. This enhanced efficiency underlines the critical role of ball rollers in optimizing material handling operations.
Choosing the Right Ball Roller for Your Needs
Selecting the appropriate ball roller is crucial for optimizing material handling operations. Start by considering factors like weight capacity, as each ball roller is designed to handle specific loads. Ensure the diameter matches your application's requirements, as it impacts load distribution and maneuverability. The surface material, such as stainless steel, is another important consideration. Stainless steel is preferred for its durability and resistance to corrosion, making it ideal for environments exposed to moisture or chemicals.
Various material and construction options are available to meet different operational needs. Stainless steel ball rollers, for example, offer exceptional longevity and reduced maintenance due to their anti-corrosive properties. Alternatively, nylon or plastic variants provide quieter operation and are well-suited for less demanding applications. Each material type has its benefits, and selecting the right one ensures efficiency, longevity, and cost-effectiveness in your handling system.
Featured Products: Ball Rollers to Optimize Your Material Handling
Versatility and efficiency in material handling are made possible with the Factory OEM Service ZBCHJJ ball rollers. These rollers are ideal for manufacturers looking for reliable components for material transfer. They offer a seamless operation with specifications tailored to industrial needs, such as polyurethane construction for low noise and stainless steel bearings for robust performance. Their ability to handle a wide range of weights makes them indispensable for industries seeking to improve productivity without compromising quality.
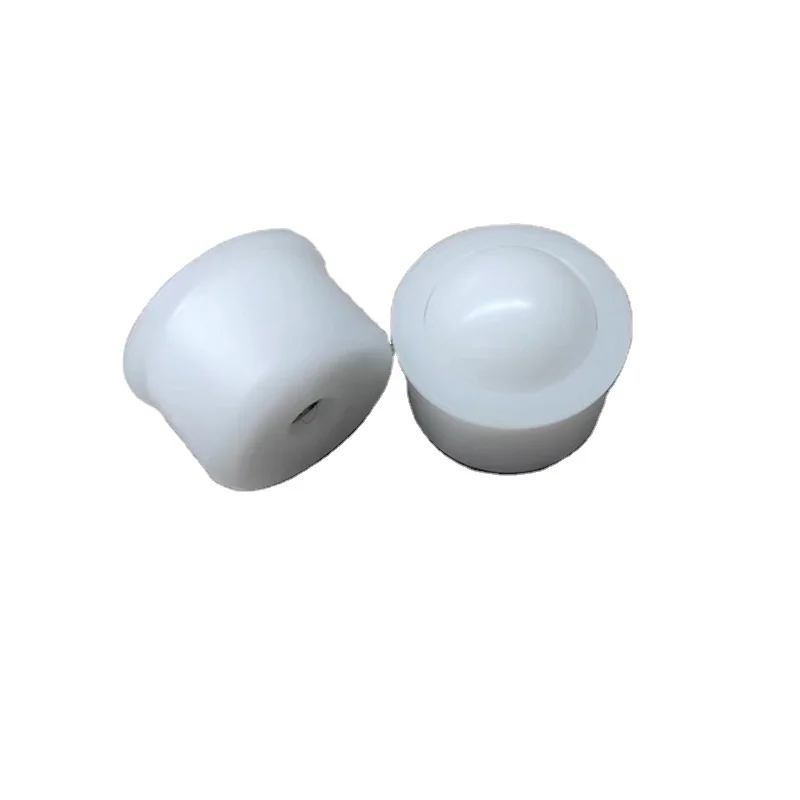
The Professional Supplier ZBCHF ball rollers excel in quality and application versatility across numerous sectors such as logistics, packaging, and assembly lines. Manufactured from high-grade materials like SUS304 stainless steel, these rollers are built to withstand challenging conditions while maintaining smooth operations. Their adaptability makes them a prime choice for businesses intent on integrating reliable, multi-functional components into their systems.
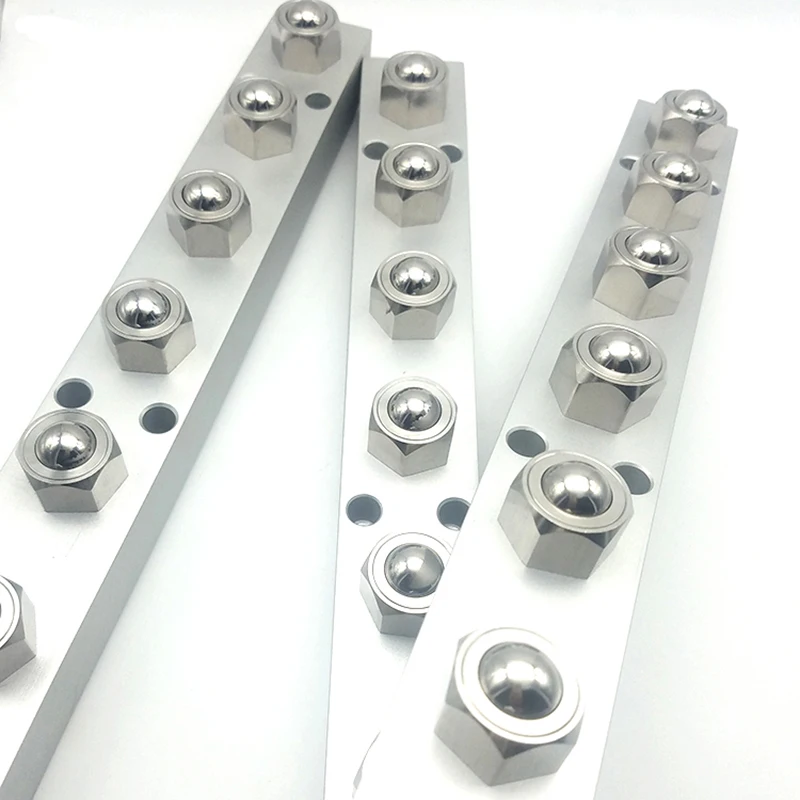
For those focused on durability and reduced maintenance, the Stainless Roller Ball Roller Units offer a distinct advantage. Featuring stainless steel construction with press fit designs, these rollers are engineered to handle extensive use with minimal upkeep. They stand out in the market due to their competitive pricing while guaranteeing performance and reliability, attracting attention from sectors that demand robust and long-lasting material handling solutions.
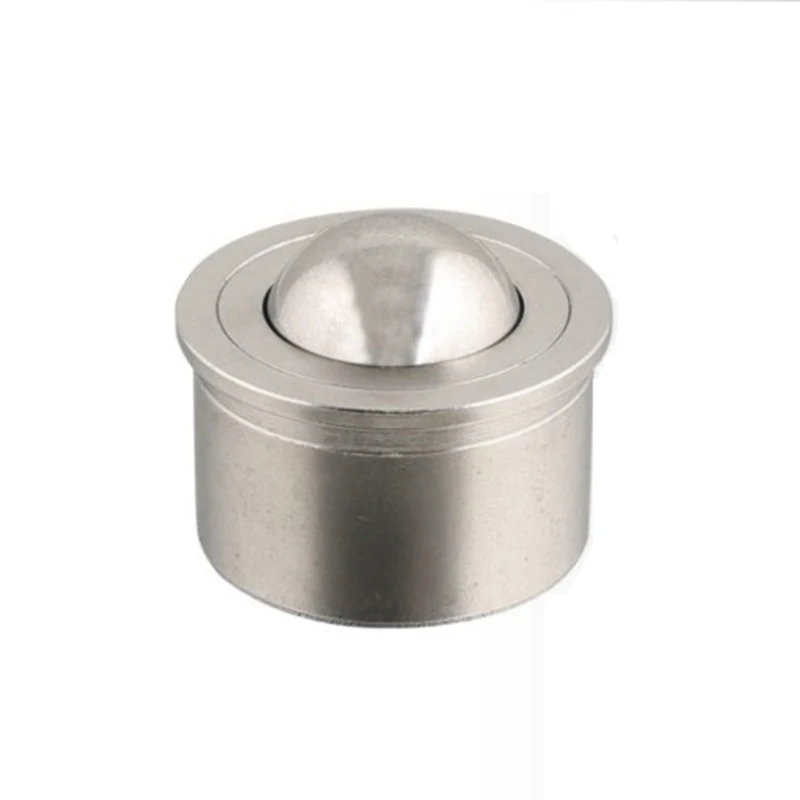
Installation and Maintenance Tips for Ball Rollers
Proper installation and maintenance of ball rollers are crucial to ensure their optimal performance and longevity. During setup, it is essential to focus on precise alignment and load distribution. Begin by ensuring that each ball roller is evenly aligned with respect to the surface it interacts with. This alignment prevents uneven wear and tear, maximizing efficiency. Additionally, make sure that the load is distributed evenly across all ball rollers to avoid overloading any single unit, which could lead to premature failure.
Routine maintenance is equally important in maintaining the functionality of ball rollers. Regular lubrication plays a pivotal role in reducing friction and preventing damage. Use the appropriate lubricant recommended by the manufacturer to keep the rollers in top condition. Additionally, schedule frequent inspections to check for any visible wear or alignment issues. Early detection of such problems can prevent costly repairs and downtime. These practices not only enhance the performance of the ball rollers but also extend their lifespan significantly.
Future Trends in Material Handling with Ball Rollers
The future of material handling with ball rollers is being shaped by technological advancements that enhance their design and functionality. Automation is playing a pivotal role in this evolution, where the integration of IoT (Internet of Things) technology allows for real-time monitoring and data analysis of ball roller operations. This enables predictive maintenance, reducing downtime and optimizing performance. Furthermore, innovations in sensor technologies are leading to the development of smart ball rollers that can self-adjust to varying weights and surfaces, ensuring efficiency and durability.
Sustainability is also a critical trend influencing material handling practices. The use of eco-friendly materials in ball rollers is becoming increasingly popular, aligning with global efforts to reduce carbon footprints. Manufacturers are exploring the use of recycled or biodegradable materials for housing and components, ensuring less environmental impact. Additionally, energy-efficient operations are supported by ball rollers through reduced friction, leading to lower energy consumption. This combination of technological advancements and sustainable practices not only enhances operational efficiency but also contributes to broader environmental goals, making ball rollers a promising component in the future landscape of material handling.